LA FONDERIE A MODELE EN CIRE PERDUE :
Notre Processus industriel
PRECIMETAL a mis en place et poursuit un plan d’investissement volontariste afin d’offrir au client une infrastructure industrielle moderne lui assurant que ses pièces seront réalisées dans un cadre qualitatif parfait avec une garantie de reproductibilité maximale et la meilleure productivité / compétitivité possible.
Les équipements font l’objet de maintenance préventive, de contrôle de sécurité périodiques et, le cas échéant, de rénovation et améliorations afin de disposer d’un parc machine de plus en plus efficace et fiable.
De la conception au prototype
- Assistance à la conception.
- Réalisation des plans d’outillages, de contrôle et d’usinage.
- Suivi de fabrication des prototypes.
- Contrôle des pièces-type à 100% y compris RX.
Planification de production – Logistique
- Lancement en « just in time ».
- Suivi de production en temps réel.
- Procédure de gestion des retards.
- Relances automatiques.
- Système automatique d’ordonnancement de production en fonction des gammes et des temps opératoires, des délais et de la charge globale.
- Mouvements physiques des fabrications par convoyeurs robotisés.
- Intégration des finitions en sous-traitance dans le cycle de fabrication.
Réalisation des modèles en cire
- Presses manuelles et automatiques programmables pour les modèles en cire.
- Changement rapide d’outillage (SMED).
- Autocontrôle permanent.
- Toutes techniques de noyautage pour contre dépouilles.
Carapaces réfractaires
- Robots automatiques de trempage / stucage.
- Système automatique de changement de cycle de programmation en fonction de la pièce (flexible manufacturing), gestion des pièces critiques.
- Produits réfractaires de haute qualité avec réception qualitative et traçabilité.
Cuissons des carapaces et coulée du métal
- Deux lignes de cuisson/fusion.
- Fours de 150, 120 et 60 Kg, four à retournement de 25Kg.
- Contrôle de la composition du métal par spectromètre d’émission.
Elimination du réfractaire
- Décocheuses à jet d’eau à haute pression.
- Grenailleuses à programmation différenciée.
- Dissolution chimique par bain de sel à 600°C.
- Sablage manuel ou automatique, à la pièce ou en vrac.
Finition
- Tronçonnage et élimination de l’attaque ; équipements automatiques ou manuels.
- Traitements thermiques simples ou complexes, in situ ou en sous-traitance.
- Compactage Isostatique à Chaud (HIP).
- Mise en forme définitive aux cotes imposées par calibrage manuel ou à la presse, à chaud ou à froid, en autocontrôle à 100%.
Contrôle
- Contrôles effectués selon les desiderata des clients.
- Machine tridimensionnelle CNC avec fonction scanner et caméra.
- Projecteur de profil avec programme informatique associé.
- Duretés, Microscope métallographique (X 800), Rugosimètre.
- CND certifiés Nadcap®:
- Rayons X (300kV) à lecture digitale.
- Ressuage fluorescent (sensibilité S2).
- Magnétoscopie en lumière noire.
- Laboratoire.
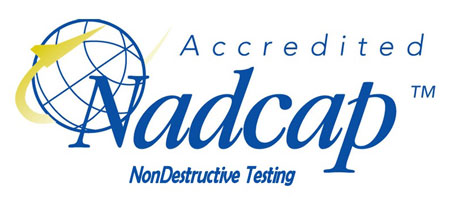
- Tous les essais mécaniques statiques et dynamiques, ainsi que des essais spécifiques (étanchéité, …) sont effectués par des laboratoires indépendants spécialisés qualifiés par les instances officielles belges (BELCERT).
Le procédé de fonderie
Origines du Procédé
La fonderie de précision, dite « à la cire perdue » est un procédé ancestral né il y a plus de 3000 ans en Mésopotamie qui ne s’appliquait qu’à des applications de bijouterie, de prothèses dentaires, de pièces artistiques, etc….
Elle nait au niveau industriel après la seconde guerre mondiale grâce à l’essor de l’armement, des engins de transport et de l’aéronautique.
Le développement de matériaux réfractaires ainsi que l’utilisation de plus en plus répandue des alliages coûteux (base nickel) et/ou difficilement usinables, lance le procédé de la cire perdue dans le monde industriel.
En effet, permettant d’obtenir des pièces de formes complexes et de cotes étonnamment précises, ce type de fonderie s’adapte bien à ces nouveaux besoins.
Depuis, elle n’a cessé de progresser et de se développer dans de nombreux secteurs d’activités.
Le procédé en bref
Le principe consiste à réaliser, à l’aide de moules d’injection métalliques, dans une matière fusible (de la cire), la réplique exacte – appelée modèle – de la pièce finale. Chaque modèle injecté donnera au final une pièce en métal. Ainsi, si le besoin est de 500 pièces, il faut injecter 500 modèles en cire.
Ces modèles sont ensuite collés sur des barreaux, en cire également, ce qui constitue des ensembles appelés grappes.
Ces grappes sont ensuite revêtues de couches de céramique par des opérations successives de trempage dans des bains de céramique et de saupoudrage sous des sables réfractaires.
Environ 6 à 10 couches sont ainsi constituées ce qui forme une carapace de l’ordre de 5 à 10mm d’épaisseur qui enrobe complètement toutes les pièces de la grappe en cire.
Après un temps de séchage, cette grappe est ensuite chauffée ce qui permet de faire fondre la cire et d’obtenir ainsi un moule céramique creux dans lequel le métal fondu sera ensuite coulé.
Ce moule réfractaire est ensuite mis dans un four à environ 1000°C pendant 1 à 2 heures, ce qui permet à la fois la cuisson du moule, l’élimination des éventuels résidus de cire et la mise à température de ce moule pour favoriser la coulée du métal en fusion.
En parallèle, le métal est mis en fusion dans des fours à induction, entre 1500 à 1600°C pour les alliages de fer, cobalt ou nickel.
Lorsque le moule est à température et que le bain de fusion est prêt, on coule le métal dans la grappe par gravité et l’on attend ensuite que l’ensemble se refroidisse.
La carapace est ensuite éliminée par action mécanique ou chimique, les pièces sont détachées de la grappe par tronçonnage.
Reste pour finir à faire le parachèvement comportant des opérations d’arasage, sablage, traitement thermique, … ainsi que les contrôles visuels, dimensionnels et non destructifs (RX, ressuage).
Cette technique est principalement utilisée pour des réalisations de pièces de formes complexes, nécessitant un excellent état de surface et une précision dimensionnelle très serrée. Elle constitue souvent une alternative intéressante à la technique de l’usinage hors masse ou de l’assemblage par soudure et est parfois un passage obligé pour des pièces comportant des cavités internes, des voiles minces, des évidements et allègements, des renforts, etc. … Elle est particulièrement efficace pour la réalisation de pièces d’acier d’un gramme à plus de 50 kg.
Toutes les nuances d’acier et alliages de cuivre, nickel et cobalt peuvent être coulés selon ce procédé. Des pièces en titane ou super alliages peuvent être également obtenues par ce procédé mais avec l’utilisation de techniques spéciales de coulées sous vide ou centrifuges.
Les avantages du procédé
Grande liberté de conception des pièces
La matière et la forme de la pièce peuvent être déterminées librement en fonction de son utilisation.
Les contraintes liées aux autres procédés disparaissent : contre-dépouilles, évidements inaccessibles par un outil classique, formes complexes dans les trois plans, … sont réalisables en fonderie de précision grâce à l’utilisation de diverses techniques de noyautage.
Usinages réduits ou supprimés
- Excellent état de surface (meilleur que Ra 6,3).
- Aspect sablé ou grenaillé propre et homogène.
- Polissage mécanique ou chimique facilité.
- Gain de rendement dans le domaine du transport de fluide.
- Surfaces directement fonctionnelles en applications hydrauliques et pneumatiques.
- Respect des normes d’hygiène en agroalimentaire.
Etat de surface dès la coulée
- Tolérances serrées (+/- 0,7% sur cotes fonctionnelles).
- Obtention directe par coulée des marquages, rainures, dentures, …
- Reproductibilité parfaite des petits détails.
- L’ absence de copeaux réduit le coût des pièces en alliage coûteux.
- Utilisation de matières difficilement usinables.
Suppression de soudure et d’assemblage
Des pièces normalement composées de plusieurs éléments peuvent être coulées en une pièce unique.
Les soudures et mise en forme par matriçage sont des sources de rupture et de coûts évitables (de meulage des cordons de soudure par exemple) par une conception du sous-ensemble directement en une seule pièce coulée.
La seule contrainte pour PRECIMETAL est que le volume de la pièce s’inscrive dans un cube de 500 mm de côté.
Diminution de poids
Les allègements, évidements et renforts permettent des gains substantiels de poids tout en garantissant la rigidité de la pièce.
Les parois peuvent être réduites à moins d’un millimètre d’épaisseur localement.
La méthode est particulièrement indiquée pour des composants à rapport de surface sur volume élevé.
Très grand choix d’alliages ferreux et non ferreux
Une centaine d’alliages en stock et une expérience pour 200 nuances d’aciers, inox et d’alliages de cobalt, nickel et cuivre.
Niveau qualitatif élevé
Les pièces obtenues par ce procédé ont une structure isotrope, c’est-à-dire que les caractéristiques mécaniques, notamment la résistance à la traction et la ductilité, ont la même valeur dans toutes les directions contrairement aux pièces forgées ou laminées dont la structure du métal est modifiée par la technique de mise en forme pas toujours compatible avec les besoins en résistance de l’utilisateur.
Faible coût d’outillage, modifications peu onéreuses et durée de vie pratiquement illimitée
L’outillage – ou moule d’injection – peut être conçu selon différentes techniques qui influenceront son prix de revient et évidemment sa longévité.
Le procédé est déjà compétitif à partir de petites séries grâce à un moule d’injection à faible coût.
En concédant un investissement plus important, il est possible de concevoir un outillage plus résistant, multi-empreintes ou automatisé : les grandes séries seront donc produites à qualité constante à moindre coût unitaire.